UNOX & OASES System Simulation Software
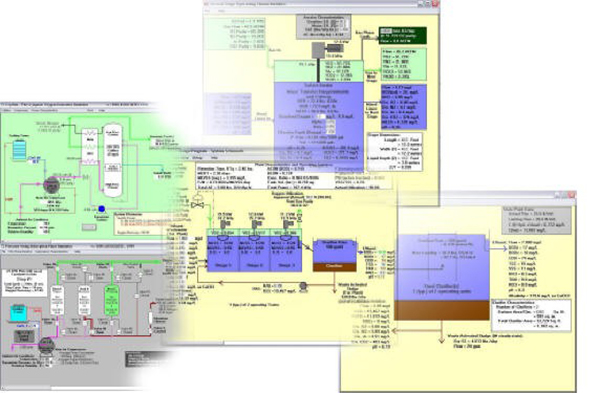
DWG ASSOCIATES not only understands high-purity oxygen (HPO) wastewater technology, we can model it and we can simulate it. Our simulators are accurate, realistic, and specifically developed to mimic HPO wastewater treatment plants. That means a covered, staged aeration basin where the feed gas and mixed liquor flow concurrently through the reactor.
For 35 years, DWG ASSOCIATES’ wastewater simulation software has been the only user friendly wastewater treatment plant simulation software that truly replicates high-purity oxygen (HPO) covered aeration basins and oxygen generation systems. DWG ASSOCIATES’ personnel have been developing HPO treatment plant software since the 1970s. Members of our staff wrote the HPO process design software that has been (and still is) used to design virtually every UNOX or OASES HPO secondary system in the world. Our first plant simulators were used in the early 1990s to provide a simulated "hands-on" operating experience for attendees at DWG ASSOCIATES’ operator training courses given in conjunction with the Georgia Institute of Technology in Atlanta, Georgia, USA. Our understanding of HPO wastewater treatment and oxygen supply will assure that you will never have to scratch your head and wonder if a diffused-air BioWin (or any other generic) model really simulates your covered HPO tanks with their elevated oxygen gas space purities (Spoiler Alert: none of them do!).
Like all simulators, ours are used for plant design, plant troubleshooting, plant optimization, operator training, and for all manner of "what if" operating scenario analyses. We’ve got simulators for HPO aeration basins, PSA oxygen generation systems, and cryogenic oxygen generation systems. Our simulation capabilities allow us to analyze your secondary system without interrupting actual plant operations; oftentimes from an off-site, remote location. And our understanding of your control system and how it affects optimum operation will ensure you that the answers we generate are backed by years of working with your specific HPO technology.